News: 2025
News: 2024
An Exclusive Product Premiere: Rajoo Launches PROEX - Series of High-Performance Blown Film Line
News: 2023
News: 2021
News: 2018
News: 2016
News: 2015
News: 2011
- Rajoo - a complete line for PP spun bond nonwoven: Jul, 2011
- Rajoo's success in Turkey- 7 layer blown film line: Jun, 2011
- India's first 3-layer co-extruded blown film line: Apr, 2011
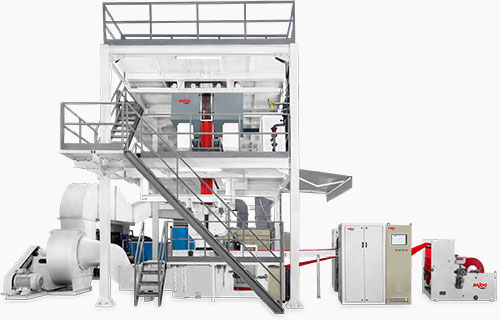
Rajoo - a complete line for PP spun bond nonwoven: Jul, 2011
Enabling India - a complete line for PP spun bond nonwoven fabric - Rajoo ushers in a new technology
With India on the anvil to embrace usage of nonwovens, this technology solution from Rajoo would go a long way in helping increase the current per capita consumption – a parameter closely linked to economic development and per‐capita income.
Across sectors, the industry is poised to witness radical changes in the adoption of PP Spun bond and melt‐blown nonwoven fabrics. Segments such as automotive, medical, personal care and hygiene, home furnishings, household, stationery, agriculture and geotextiles would be the early adopters and enjoy the benefits presented by use of nonwovens as:
- Fabrication speed and flexibility
- Can be slit in both directions without fraying
- Heat sealed / seamed / folded / shaped in a variety of ways
- Possibility of ultrasonic welding
Understanding this market opportunity and industry benefit, Rajoo Engineers decided to address the areas relating to low productivity and cost competitiveness as well as obsolete technology by launching a Complete Line for Producing PP Spun Bond and Melt‐blown Nonwoven Fabric. With India on the anvil to embrace usage of nonwovens, this technology solution from Rajoo would go a long way in helping increase the current per capita consumption – a parameter closely linked to economic development and per‐capita income
Nonwoven fabrics present substantial advantages. Manufactured by high speed low cost processes, nonwovens are even today used in many applications, most of them hidden. For medical applications they not only offer high absorbency and airpermeability, but also do not stick to the wound ensuring a skinfriendly micro‐climate. In furniture and textile applications, nonwovens excel in terms of their look, permeability and abrasion resistance. The structure and low weight of acoustic nonwovens offer significant advantages in perforated ceiling systems when compared to conventional sound-proofing systems. Nonwovens in horticultural protect plants against temperature extremes by day and night, thus creating a foundation for earlier harvests with excellent results. In addition to being air and water permeable, they can be UV stabilised and are resistant to rotting. In window treatments, nonwovens are used to design windows for enhanced functionality and appearance. Their ability to diffuse light while maintaining room brightness enhances the feeling of privacy and helps protect furniture. Their natural insulating ability helps in energy conservation. This partial list of ever growing applications is a clear signal of the fast acceptance of this fabric, primarily due to its unique properties.
The spun bonded process direct extrusion followed by online thermal web bonding is the most versatile and popular process. The Rajoo solution, built on a similar line includes:
- Primary extruder
- Trim recycling extruder
- Automatic screen changer
- Melt pump, Barmag
- Spinnerets
- Filament cooling / Fibre quenching
- Filament stretching / Draw bench
- Web forming
- Thermal bonding
- Winding
- Slitter re‐winder
- Chillers
- Vacuum furnace / Calciner
- Ultrasonic cleaner
- Touch screen control panel
About Rajoo
Based in Rajkot, Rajoo Engineers Limited, having made a modest beginning in 1986, has today emerged as an undisputed global player in blown film and sheet extrusion lines. Owing to its focused efforts in blown film and sheet extrusion lines, the Company enjoys premium market position in this segment. Being a technology driven Company, product innovations, world-class quality, state-of-the-art workmanship, increased energy efficiency, and high levels of sophistication and automation have become the hallmark of Rajoo products during all these years, positioning the Company's products on a global platform, competing with the established world leaders. With representations in many countries of the world and customers in over 53 countries, the Company's exports have multiplied after its debut in the international market in 1990. (www.rajoo.com)
For further details please contact:
Khushboo Doshi
Head-Marcom
Phone: +91 2827 252701/2/3
Fax: +91 2827 252700
Email: info@rajoo.com
Website: www.rajoo.com
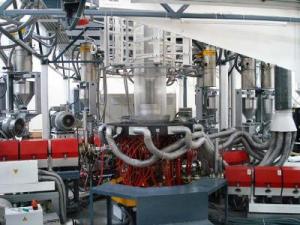
Rajoo's success in Turkey- 7 layer blown film line: Jun,2011
Rajoo celebrates success in Turkey with supply of Asia's first fully automatic 7 layer blown film line
Sahin Plastik ‐ Vakum, Turkey clearly saw immense value in this purchase from Rajoo. Totally customised, this solution addressed every need of Sahin and ensured that Sahin has just the right product, and thus, at just the right price.
Rajoo Engineers created history by being the first supplier of a 7‐layer fully loaded Blown Film Line from Asia.
Fully loaded 7 layer blown film line This landmark sale and successful commissioning at Sahin Plastic‐Vakum, Turkey – is in a market that was till now considered a strong‐ hold of leading extrusion machinery manufacturers from Europe. It is an endorsement of the high quality standards maintained by Rajoo and a salute to the indomitable spirit of the quality of Indian manufacturing.
Sahin clearly saw immense value in this purchase from Rajoo. Totally customised, this solution addressed every need of Sahin and ensured that Sahin has just the right product, and thus, at just the right price. This machine is primarily being used to produce barrier films, retort packaging films, lidding films for vacuum forming applications, etc.
‘This latest feather in Rajoo’s cap clearly annunciates the road ahead for Rajoo Engineers, with the world as its market place’, says Sunil Jain, President Rajoo Engineers.
Technology and Quality – Key Differentiators
- This 7‐layer CE compliant plant is with 2 x 60 mm grooved feed extruders (A, G), 2 x 50 mm grooved feed extruders (C, E) and 3 x 40 mm smooth-bore extruders (B, D, F). It is equipped with a 400 mm UCD® die (stack type with horizontal melt flow paths) and an IBC system.
- To ensure precise & accurate blend and gsm control of the film, the machine is equipped with gravimetric feeding and blending of 7 main components, 11 secondary components and integrated conveying systems for 18 materials.
- In addition, the machine also incorporates an automatic film thickness control system with segmented disc to control one of the most critical parameters in blown film applications. The thickness is measured using two solid state high definition noncontact capacitive sensors with 0.1 micron resolution especially designed for nylon and EVOH based barrier films. The sensors are mounted on a rigid O‐frame scanner, which in turn is mounted after the nip rollers when the film is substantially cooler. The film is wound on a back‐to‐back dual‐station load cell controlled surface winder with taper tension control producing large diameter rolls of upto 1000mm.
The machine is operated through an integrated touch‐screen based supervisory control system for all the machine parameters such as:
- Processing temperatures
- Extruder speeds
- Automatic screen changer
- Melt temperature and pressure
- IBC
- Calibrating basket diameter and height
- Oscillating haul‐off speed
- Material recipes
- Historic data recall
The machine is effortlessly producing at Sahin’s Factory, a 200‐micron barrier film with 50 micron nylon and 1010 mm lay‐flat width, providing an output of 240 kg/hour, thickness variation under ± 3% on 2‐sigma and width variation of less than ±3 mm.
The delighted owner of Sahin Plastik‐Vakum is proud of his decision and declares that he is happy and contented with the performance of the machine and will continue to buy from Rajoo in future.
About Rajoo
Based in Rajkot, Rajoo Engineers Limited, having made a modest beginning in 1986, has today emerged as an undisputed global player in blown film and sheet extrusion lines. Owing to its focused efforts in blown film and sheet extrusion lines, the Company enjoys premium market position in this segment. Being a technology driven Company, product innovations, world-class quality, state-of-the-art workmanship, increased energy efficiency, and high levels of sophistication and automation have become the hallmark of Rajoo products during all these years, positioning the Company's products on a global platform, competing with the established world leaders. With representations in many countries of the world and customers in over 53 countries, the Company's exports have multiplied after its debut in the international market in 1990. (www.rajoo.com)
For further details please contact:
Khushboo Doshi
Head-Marcom
Phone: +91 2827 252701/2/3
Fax: +91 2827 252700
Email: info@rajoo.com
Website: www.rajoo.com
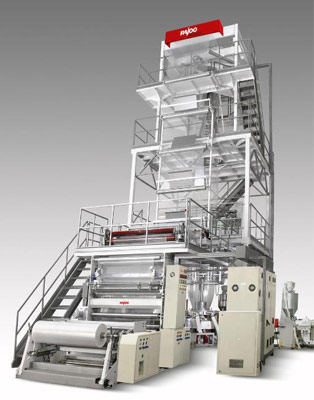
India's first 3-layer co-extruded blown film line: Apr, 2011
In a pioneering initiative, Rajoo Engineers becomes the first Indian company to supply a 3-layer co-extruded blown film line to Pakistan. Traversing this distance from Rajkot to Lahore, Rajoo has created a significantly tailored solution that addressed all needs of Polypack Pvt. Ltd. Rajoo, a globally known extrusion machine manufacturer for delivering highly customised solutions, surpassed expectations of Polypack by providing a solution on similar lines, well understanding their basic needs.
Polypack Pvt. Ltd., Pakistan, one of the most renowned names in Pakistan’s emerging flexible packaging market took this decision after thorough evaluation of all options. Already extruding plastic films on monolayer and two layer blown film plants from various sources, they chose to ignore cheaper variants in favour of Rajoo on understanding the value proposition that is a part of every ‘Rajoo Machine’.
‘For Rajoo, this sale provides a significant entry into the Pakistan market by being the supplier of a multilayer blown film plant to Polypack, one of the largest manufacturers of polypropylene woven sacks in Lahore as the first reference,’ says Sunil Jain, President, Rajoo Engineers.
Since Pakistan is a growing economy, this landmark sale will present immense opportunities for Rajoo to cater to this market. With the Rajoo’s 3-layer co-extruded blown film line, Polypack finds a true and totally customised solution to address all its needs – film for liquid packaging, stretch film, shrink film and lamination grade film. ‘The Rajoo product, quality, service and an overall handholding were aspects that added immense value to Polypack, giving them confidence,’ added Sunil. As with the changing environment, the Rajoo – Polypack relationship is all set to create new definitions in business and customer delight.
The 3-layer co-extruded blown film line installed at Polypack in Lahore is equipped with 2 x 50 mm and 1 x 60 mm grooved feed barrier extruders. The machine is with fully automatic load cell based tension controlled surface winder. To compensate lasting thickness irregularities which cannot be prevented, the take-off unit is furnished with an oscillating haul-off unit. The liquid PIB Dosing unit will help to produce Stretch and Cling film in a cost effective manner, instead of using traditional masterbatches.
In addition to other film products, the machine is designed to produce 37.5 micron film with 1500 mm lay flat width and output of 250 kg/hr with thickness variation of under ±8% to cater into various applications including packing of water, edible oil & ghee, shrink film etc.
About Rajoo
Based in Rajkot, Rajoo Engineers Limited, having made a modest beginning in 1986, has today emerged as an undisputed global player in blown film and sheet extrusion lines. Owing to its focused efforts in blown film and sheet extrusion lines, the Company enjoys premium market position in this segment. Being a technology driven Company, product innovations, world-class quality, state-of-the-art workmanship, increased energy efficiency, and high levels of sophistication and automation have become the hallmark of Rajoo products during all these years, positioning the Company's products on a global platform, competing with the established world leaders. With representations in many countries of the world and customers in over 53 countries, the Company's exports have multiplied after its debut in the international market in 1990. (www.rajoo.com)
For further details please contact:
Khushboo Doshi
Head-Marcom
Phone: +91 2827 252701/2/3
Fax: +91 2827 252700
Email: info@rajoo.com
Website: www.rajoo.com
News: 2010
- Rajoo Engineers - technology leap at K-2010: Nov, 2010
- Rajoo Engineers Limited in Business India: Nov, 2010
- Rajoo Engineers and Hosokawa Alpine AG, Germany: Oct, 2010
- Rajoo Engineers JV with Bausano of Italy: Oct, 2010
- Rajoo - Wonder pack Align: Jun, 2010
- Rajoo at Plastex 2010, Egypt: Jun, 2010
- Distinctive distinction: Shree Yantralay by Rajoo: May, 2010
- PS foam extrusion lines from Rajoo Engineers Ltd.: Jan, 2010
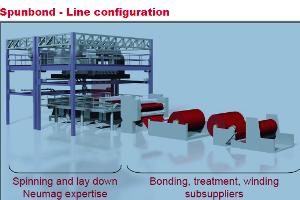
Rajoo Engineers - technology leap at K-2010: Nov, 2010
The year 2010 as it is, has already been a landmark year for Rajoo – the merger with Wonder pack, the technical collaboration with Hosokawa Alpine and the joint venture with Bausano and Figli, Italy…the industry could not have asked for more!
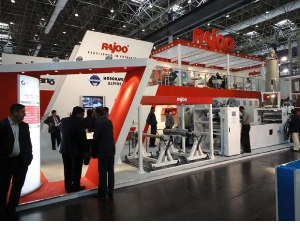
Rajoo's stand at K-2010
For Rajoo Engineers, K 2010 was extremely different, as expected. As usual, Rajoo’s booth in the extrusion section, including that of Wonder pack amongst the thermoformer manufacturers, stood out in clean white with judicious use of red ‐ a result of fine aesthetics, impressive presentation of the workmanship and style ‐ a feature synonymous with Rajoo.
The year 2010 as it is, has already been a landmark year for Rajoo – the merger with Wonder pack, the technical collaboration with Hosokawa Alpine and the joint venture with Bausano and Figli, Italy…the industry could not have asked for more!
These news made headlines in international circles and turned out to be one of the most talked‐about topics during the recently concluded K 2010 in Dusseldorf, Germany.
To mark this new beginning, the Rajoo booth was inaugurated on the first day of the show on October 27, 2010, by Peter Krieg, President, Hosokawa Alpine. This technical collaboration was very important news for the industry as it meant coming together of two significant companies manufacturing blown film lines for years! The Hosokawa Alpine lines are used around the world where customers demand high quality and performance. Rajoo systems meet exacting requirements (with a position of distinct leadership) in many newly industrialised countries such as India, Africa, Gulf and parts of Latin America and have their main focus on an attractive price‐performance ratio for the customers.
The year 2011 will witness the commissioning of Rajoo Bausano Extrusion Pvt. Ltd. at Rajkot ‐ the joint venture in India between Rajoo Engineers & Bausano and Figli, Italy to produce and market pipe and profile lines (including for wood composite profiles) in India and various parts of Africa, Gulf and SAARC region. With this, Rajoo and Bausano will revolutionise pipe manufacturing technology in India, furthering its commitment to bring world class technology at the door-step of the Indian processors. Pipe and profile extrusion lines with 30 L/D extruders (for enhanced homogenisation and high output levels) driven by the patented high torque ‘multi‐drive’ system with four synchronised motors (much smaller motors consuming less power with lower maintenance costs) and ‘vacuum sizing technique’ ( for improved inner pipe surface) would now be available. ‘Rajoo and Wonder pack booths experienced stupendous response ‐ much more than what we expected. The concept of hybrid blown film lines at affordable price levels to be offered by Rajoo and Hosokawa Alpine generated a lot of interest amongst blown film producers from India and Africa’, said Sunil Jain, President, Rajoo Engineers. ‘The Bausano technology for pipes and profiles extrusion will also be a boon for the industry ‐ a sure indication of the trends to follow in this plastic processing industry’, he added.
The rPET sheet line demonstrated at the Rajoo booth evinced great interest in the processors from all over the world – more specifically from Europe and South America. One of the only running sheet-line using 100% PET bottle flakes was producing 300 kg/hour of crystal clear PET Sheet of 700 mm wide three layer (ABA) in thickness range of 0.2 – 1 mm. The line was complete with crystalliser and dehumidifier, continuous automatic screen changer, hydraulically slid upper and lower polishing rollers with fine gap adjustment and Siemens integrated touch screen based computerised extrusion process control.
For further details please contact:
Khushboo Doshi
Head-Marcom
Phone: +91 2827 252701/2/3
Fax: +91 2827 252700
Email: info@rajoo.com
Website: www.rajoo.com
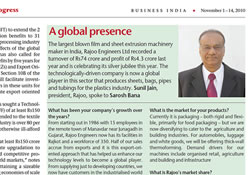
Rajoo Engineers Limited in Business India: Nov 2010
The largest blown film and sheet extrusion machinery maker in India, Rajoo Engineers Ltd recorded a turnover of Rs74 crore and profit of Rs4.3 crore last year and is celebrating its silver jubilee this year. The technologically-driven company is now a global player in this sector that produces sheets, bags, pipes and tubing for the plastics industry.
Sunil Jain, President, Rajoo, shares his vision on global plastic industry and how Rajoo is poised to maintain its one up position by offering innovative solutions to global marketplace.
You can read complete story here.
For further details please contact:
Khushboo Doshi
Head-Marcom
Phone: +91 2827 252701/2/3
Fax: +91 2827 252700
Email: info@rajoo.com
Website: www.rajoo.com
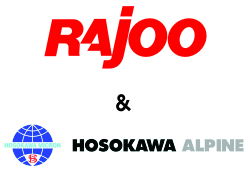
Rajoo Engineers and Hosokawa Alpine AG, Germany: Oct, 2010
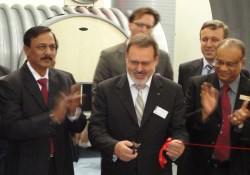
The markets in India and parts of Africa, would benefit immensely with this collaboration. It would bring the very best in blown film technology of HOSOKAWA ALPINE through one of the most trusted and respected names in the business – Rajoo Engineers.
The maxim ‘Excellence in Extrusion’ continues to drive Rajoo Engineers and thus the technical collaboration with HOSOKAWA ALPINE AG of Germany – one of the most reputed companies globally in this sector – comes as no surprise.
Both companies are long‐established manufacturers of blown film lines. The HOSOKAWA ALPINE lines are used around the world by customers with high quality and performance demands. The RAJOO systems cover the demands in many newly industrialised countries such as India, Africa, Gulf and parts of Latin America and have their main focus on an attractive price‐performance ratio for the customers.
The markets in India and parts of Africa (Nigeria, Ghana, Kenya and Tanzania), would benefit immensely with this collaboration. It would bring the very best in blown film technology of HOSOKAWA ALPINE through one of the most trusted and respected names in the business – Rajoo Engineers at affordable price levels.
In a first step, Rajoo Engineers Ltd. will assume responsibility for marketing and service support for Alpine’s blown film systems in India as well as in Nigeria , Ghana, Kenya and Tanzania. Both companies plan to jointly develop a new product line of blown film systems. It is planned to combine the time proven machine components of both manufacturers to form new hybrid systems on a higher quality level and at a simultaneously attractive price levels. In future, this joint venture will be extended to include co‐operation in the areas of service support, development, production, joint procurement and sales and marketing.
‘Rajoo’s strong understanding of the developing economies coupled with world class technology of Alpine will ensure a unique mix that customers would benefit from, says Sunil Jain, President, Rajoo Engineers. ‘The brand and the network of Rajoo will only raise the bar of customer satisfaction’, he adds. This alliance with ALPINE would only further the focused efforts of Rajoo in blown film lines, an area where the company enjoys premium market position.
‘Synergies will result from this cooperation in the areas of international marketing, production and procurement as well as in joint product development. For Alpine, this collaboration would also serve as an extension of its manufacturing capability, wherein it could now source from India, aggressively priced blown film solutions (using its technology and manufactured by Rajoo Engineers), for its global markets.’, says Peter Krieg, President, Hosokawa Alpine AG.
The existing Rajoo portfolio of the widest range of mono and multilayer blown film lines up to seven layers, sheet lines up to five layers, water quenched downward extrusion lines up to three layers, lines for foamed film and sheets for various special applications and thermoformers will now be supplemented by hybrid products as well as complete ALPINE systems, giving the customer enough options to choose from.
About Rajoo
Based in Rajkot, Rajoo Engineers Limited, having made a modest beginning in 1986, has today emerged as an undisputed global player in blown film and sheet extrusion lines. Owing to its focused efforts in blown film and sheet extrusion lines, the Company enjoys premium market position in this segment. Being a technology driven Company, product innovations, world-class quality, state-of-the-art workmanship, increased energy efficiency, and high levels of sophistication and automation have become the hallmark of Rajoo products during all these years, positioning the Company's products on a global platform, competing with the established world leaders. With representations in many countries of the world and customers in over 53 countries, the Company's exports have multiplied after its debut in the international market in 1990. (www.rajoo.com)
For further details please contact:
Khushboo Doshi
Head-Marcom
Phone: +91 2827 252701/2/3
Fax: +91 2827 252700
Email: info@rajoo.com
Website: www.rajoo.com
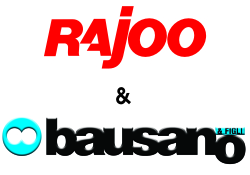
Rajoo Engineers JV with Bausano of Italy: Oct, 2010
Known for bringing world class technology at the door step of the Indian processors, with this JV (based in Rajkot), Rajoo Engineers will now revolutionise pipe manufacturing technology in India.
The spirit of ‘Innovation’ continues to charter the Rajoo Engineers growth story – a diversification into the pipe and profile extrusion machinery – through a joint venture with Bausano & Figli S.p.a of Italy, one of the most reputed companies globally in this sector. This is probably what the Indian pipe manufacturing industry has been waiting for. With lack of availability of modern equipment / technology for PVC pipe production, companies were compelled to make do with decades old technologies. This industry will now witness a major boost with this JV christened – Rajoo Bausano Extrusion Pvt. Ltd. which is a fine blend of the expansive infrastructure of Rajoo and technology of Bausano. Availability of indigenous raw material and now access to the latest in technology in India (through this JV), usher good times for the large and growing market of PVC pipe manufacturing in India to boost the developments in agriculture and infra‐structure sectors.
Bausano & Figli S.p.a started manufacturing twin screw extruders way back in 1946 and is today one of the most reputed pipe and profile extrusion machinery manufacturers in the world. Known for bringing world class technology at the door step of the Indian processors, with this JV (based in Rajkot), Rajoo and Bausano will now revolutionise pipe manufacturing technology in India. This pioneering initiative of Rajoo would surely have followers, all of which would work towards the benefit of the industry at large.
The Indian processors who currently use short extruders (18‐20L/D) will now be offered Rajoo‐Bausano 30 L/D extruders to enhance melt homogenisation at much higher output levels using similar size extruder and motor ratings. The rough inner pipe surface, a result of the sizing done using the ‘floating bung technique’, will also be a thing of the past with ‘vacuum sizing’ technique (resulting in lower energy consumption for the farmers while transporting water) that is used by Rajoo‐Bausano. The patented high torque ‘Multi‐Drive’ system with four synchronised motors driving the Rajoo‐Bausano extruder with much smaller motors, consume less power with lower maintenance costs.
With operations scheduled to commence in 2011, Rajoo Bausano Extrusion Pvt. Ltd. will produce and market pipe and profile lines (including for wood composite profiles) in India and various parts of Africa, Gulf and SAARC region.
The existing Rajoo portfolio of the widest range of mono and multilayer blown film lines up to seven layers, sheet lines up to five layers, water quenched downward extrusion lines up to three layers, lines for foamed film and sheets for various special applications and thermoformers will now be supplemented by pipe and profile extrusion lines .
About Rajoo
Based in Rajkot, Rajoo Engineers Limited, having made a modest beginning in 1986, has today emerged as an undisputed global player in blown film and sheet extrusion lines. Owing to its focused efforts in blown film and sheet extrusion lines, the Company enjoys premium market position in this segment. Being a technology driven Company, product innovations, world-class quality, state-of-the-art workmanship, increased energy efficiency, and high levels of sophistication and automation have become the hallmark of Rajoo products during all these years, positioning the Company's products on a global platform, competing with the established world leaders. With representations in many countries of the world and customers in over 53 countries, the Company's exports have multiplied after its debut in the international market in 1990. (www.rajoo.com)
For further details please contact:
Khushboo Doshi
Head-Marcom
Phone: +91 2827 252701/2/3
Fax: +91 2827 252700
Email: info@rajoo.com
Website: www.rajoo.com
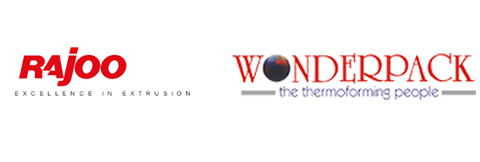
Rajoo - Wonder pack Align: Jun, 2010
Rajoo and Wonder pack align: a unified approach for the benefit of the therforming industry
For Rajoo Engineers Ltd. (Excellence in Extrusion) and Wonder pack Industries Pvt. Ltd (The Thermoforming People), this endeavor highlights the common mindset and approach of both companies, which is to be recognized as a quality global supplier for the thermoforming industry. The companies now come together with a new approach to serve the sheet extrusion and thermoforming industry, worldwide. The merged entity will now truly qualify to provide ‘end-to-end solutions in thermoforming’. Extrusion has always been the forte of Rajoo while thermoforming has been the core strength of Wonder pack.
Rajoo Engineers needs no introduction in the world markets and is well established as a quality manufacturer of plastic extrusion machines - mono and multilayer blown film lines ( upward and downward), mono and multilayer sheet extrusion lines, thermoformers and FPS ( foamed polystyrene) lines for disposables containers . The company continues to endeavor to further its current reach that is spread across 40 countries and to be considered as the most trusted provider of solutions for the plastic extrusion industry worldwide.
Wonder pack Industries was founded in 1985 with a focus on the development and manufacture of thermoforming machines for thin & thick wall applications, plastic packaging and compact sheet line extrusion machinery with customers in over in 40 countries under the trade name of – Wonder pack.
With a vision for steep growth and well-understanding the dynamics of the markets, this collaborative move promises to provide significant value propositions for all concerned. There would be significant benefit when the merged entity will take advantage of each other’s technology, developments, service network and marketing strengths. In the revised setup, Wonder pack will operate as a separate division of Rajoo Engineers at Nasik under the leadership of Amit Shah, the founder and Managing Director of Wonder pack now joins the Board of Rajoo Engineers.
For the industry, there will now be a wider range to choose from. In addition to the Rajoo products, the portfolio of Wonder pack that would also be available through the combined entity includes:
- Sheet extrusion with in-line thermoforming
- Thermoforming with in-line cutting and stacking
- Automatic roll fed in-line trim–in place thermoforming
- Special purpose thick walled vacuum forming
- Continuous thermoforming for thick wall applications
- Automatic vacuum/blister making machines
- Shrink wrapping machines and systems
- Thermoform fill and seal machines
C. N. Doshi, Chairman, Rajoo Engineers says, Coming together of competitors is not a new phenomenon, the objective here is to synergise and enhance the technology levels. With Amit Shah joining the Board of our Company, we will now provide the industry a single point source for a wider range of world class sheet extrusion and thermoforming systems. The entrepreneurial skills and technology prowess of Mr. Shah coupled with decades of experience of Rajoo and its worldwide presence will surely help Rajoo grow leaps and bounds’.
Amit Shah, Founder and Managing Director, Wonder pack Industries adds, ‘The industry will benefit immensely from this collaboration. I look forward to taking this combined entity to newer orbits – both in terms of technology levels and footprint and I see very certainly, it will soon become a force to reckon with at the global level’. Solutions from Rajoo and Wonder pack will continue to be available to the industry as before, albeit with more options. The selling, marketing and servicing networks of Rajoo and Wonder pack will now reinforce one another and come under one umbrella for unparalleled service levels witnessed by the industry.
The forthcoming K at Dusseldorf in October, 2010 will witness the synergistic developments of both, Rajoo and Wonder pack, now under one umbrella.
About Rajoo
Based in Rajkot, Rajoo Engineers Limited, having made a modest beginning in 1986, has today emerged as an undisputed global player in blown film and sheet extrusion lines. Owing to its focused efforts in blown film and sheet extrusion lines, the Company enjoys premium market position in this segment. Being a technology driven Company, product innovations, world-class quality, state-of-the-art workmanship, increased energy efficiency, and high levels of sophistication and automation have become the hallmark of Rajoo products during all these years, positioning the Company's products on a global platform, competing with the established world leaders. With representations in many countries of the world and customers in over 53 countries, the Company's exports have multiplied after its debut in the international market in 1990. (www.rajoo.com)
For further details please contact:
Khushboo Doshi
Head-Marcom
Phone: +91 2827 252701/2/3
Fax: +91 2827 252700
Email: info@rajoo.com
Website: www.rajoo.com
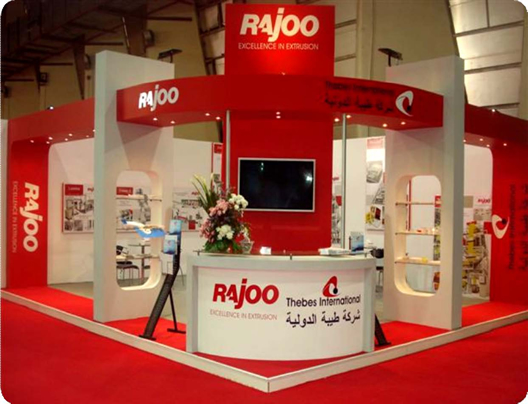
Rajoo at Plastex 2010, Egypt: Jun, 2010
Rajoo Engineers Ltd. well received by the Egyptian plastic industry at Plastex 2010
Rajoo Engineers is today considered as a quality supplier of extrusion equipment, the stupendous response at Plastex 2010 was just another endorsement.
The typical myths and beliefs, common with the Egyptian culture, were missing this time at the Plastex 2010, where the verdict was clear - a comprehensively successful event that offered significant opportunities to all exhibitors and Rajoo Engineers was no different. The event was held at Cairo, Egypt between the 13th and 16th May, 2010.
For Rajoo this was another event, systematically planned and well executed with a premiere location at Hall no. 4. The stand space was neatly spruced up as a designer booth that received applause from all those who visited. The Rajoo booth at Plastex 2010 was rated as amongst the top three along with Qapco.
Due to its sustained initiatives, Rajoo Engineers along with its local agent Thebes international, Egypt have met with resounding success in the Egyptian market which today sees a rapidly growing number of processors interested in Rajoo’s products. This event coincided with the commissioning of Rajoo’s Three Layer Co-Extrusion Blown Film line in Egypt for growing applications like mulch, stretch, cling, lamination and shrink with United Plastic Industries in Ismalia ( 150 kms from Cairo). The growing Egyptian plastic industry is becoming increasingly modernised, but is cost conscious in terms of investment, a need which Rajoo is ideally positioned to fulfill. With the demand expected to grow at 10% annually, this wealthy market in Egypt presents immense opportunities, especially in sub-sectors as flexible packaging, disposable containers and foamed PS products. Containers of rPET sheet using recycled PET bottle flakes also offers good opportunities for which Rajoo has the most appropriate value-for-money technology.
‘The Plastex 2010 has provided us with an extremely good platform to connect with the processors and offer them cost effective solutions that they would be proud of. In this, Thebes International has had a significant role to play’, says Sunil Jain, President, Rajoo Engineers. Bassem El – Melegy, Director of Thebes International who promote Rajoo machines in Egypt adds ‘The successful installation of a three layer blown film plant in Ismalia has proven that Rajoo Engineers has a lot to offer to the Egyptian market. This has boosted our confidence and we are sure of selling many more Rajoo machines in this region.’
At the show, the Rajoo stand witnessed continuous activity of serious business visitors with extended dialogues relating to future opportunities for mutual benefit.
About Rajoo
Based in Rajkot, Rajoo Engineers Limited, having made a modest beginning in 1986, has today emerged as an undisputed global player in blown film and sheet extrusion lines. Owing to its focused efforts in blown film and sheet extrusion lines, the Company enjoys premium market position in this segment. Being a technology driven Company, product innovations, world-class quality, state-of-the-art workmanship, increased energy efficiency, and high levels of sophistication and automation have become the hallmark of Rajoo products during all these years, positioning the Company's products on a global platform, competing with the established world leaders. With representations in many countries of the world and customers in over 53 countries, the Company's exports have multiplied after its debut in the international market in 1990. (www.rajoo.com)
For further details please contact:
Khushboo Doshi
Head-Marcom
Phone: +91 2827 252701/2/3
Fax: +91 2827 252700
Email: info@rajoo.com
Website: www.rajoo.com
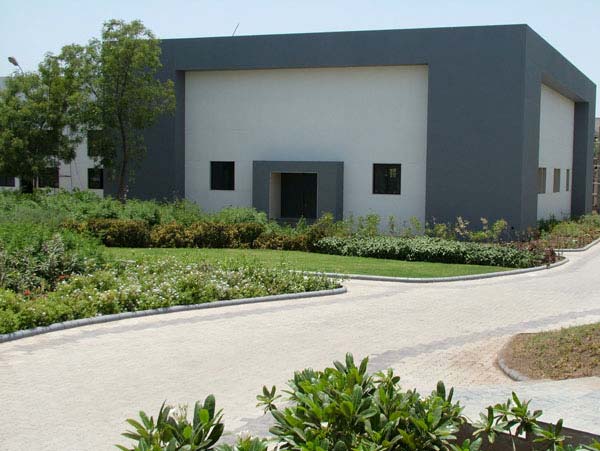
Distinctive distinction: Shree Yantralay by Rajoo: May, 2010
DISTINCTIVE DISTINCTION: RAJOO RAISES THE BAR OF WORKMANSHIP PERFORMANCE & QUALITY WITH ‘SHREE YANTRALAYA’ The state‐of‐the‐art tooling zone, Shree Yantralaya would go a long way in ensuring consistently higher accuracy levels in all critical components.
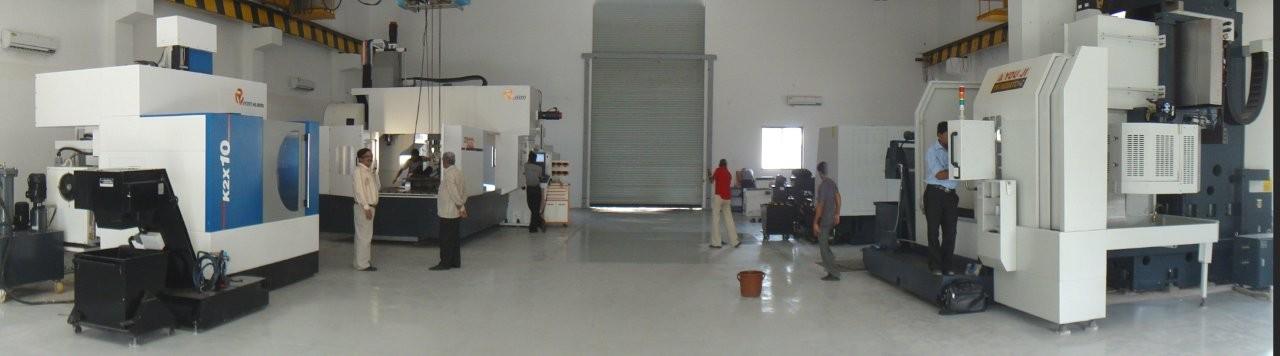
For Rajoo, being considered as ‘innovators in extrusion’ was not enough; on 15th May, 2010 Rajoo redefined the threshold for workmanship, performance and quality by inaugurating its ultra modern tooling zone christened – ‘Shree Yantralaya’ ( meaning “abode for tools dedicated to the Lord” in Sanskrit) at its Rajkot campus.
This day would be dotted in the history of Rajoo Engineers as a landmark day when the company adopted the latest in world class tooling and machining technology to provide its customers products compliant to the stringent global standards with increased levels of accuracy consistently.
Enhanced quality components produced in a controlled air conditioned and dust freeenvironment, with better workmanship, accuracy and quick turnaround are attributes that necessitated this significant investment in the conceptualisation of ‘Shree Yantralaya’ which is now the abode for machine tools such as:
- Feeler, Taiwan – 4 axis CNC Turning Centre
- Jyoti, India – CNC Turning Centre
- Huron France – Double Column Vertical Machining Centre
- Huron, France – Three Axis High Speed Milling Centre
- You Ji, Taiwan – CNC Vertical Turning Lathe
- Heckert – CNC Thread Milling Machine
- KMT, Jetline, Germany – 2 axis water jet cutting machine
- Smithson, India – Universal Cylindrical grinding machine
- Pinachio, Spain – 3 axis CNC smart turn lathe
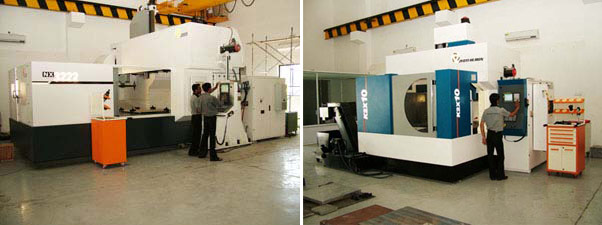
These machine tools will employ precise machining technology to produce extremely high‐quality components. Digitally designed complex component will be seamlessly transposed to these machine tools directly, eliminating the need for human intervention and related errors. ‘Shree Yantralaya’ presents an immaculate approach helping the company refine the scope of ‘Excellence in Extrusion’. Access to these latest machining technologies and techniques empowers the company to only further the customer satisfaction to greater heights.
Ninety percent of the hot parts and air ring components of the machines built by Rajoo will now be CNC machined resulting in higher repeat accuracy, quick turn around time and easy replaceability of components.
About Rajoo
Based in Rajkot, Rajoo Engineers Limited, having made a modest beginning in 1986, has today emerged as an undisputed global player in blown film and sheet extrusion lines. Owing to its focused efforts in blown film and sheet extrusion lines, the Company enjoys premium market position in this segment. Being a technology driven Company, product innovations, world-class quality, state-of-the-art workmanship, increased energy efficiency, and high levels of sophistication and automation have become the hallmark of Rajoo products during all these years, positioning the Company's products on a global platform, competing with the established world leaders. With representations in many countries of the world and customers in over 53 countries, the Company's exports have multiplied after its debut in the international market in 1990. (www.rajoo.com)
For further details please contact:
Khushboo Doshi
Head-Marcom
Phone: +91 2827 252701/2/3
Fax: +91 2827 252700
Email: info@rajoo.com
Website: www.rajoo.com
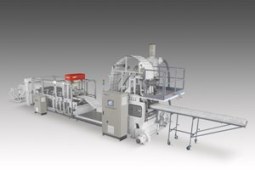
PS foam extrusion lines from Rajoo Engineers Ltd.: Jan, 2010
Being a pioneer in polymer foam extrusion in India, and with experience such that over 90% of cap liners and foamed banners in India are produced on the ‘FOMEX’ series from Rajoo Engineers; the company now meets with resounding success with ‘FOMEX – FPS’ and ‘DISPOCON-FPS’ series.
With the market for PS foam thermoformed products poised to grow at an exponential pace in India, the industry has lot to cheer. In addition, the FOMEX -FPS Foam Extrusion Lines from Rajoo, manufactured in technical collaboration with Commodore Inc., U.S.A. (world leaders in this business) provides another significant advantage, since the industry can now be confident to produce a quality product - with help of proven Foam Extrusion Lines from Rajoo, that are backed by an efficient after sales service - to address the needs of this emerging market.
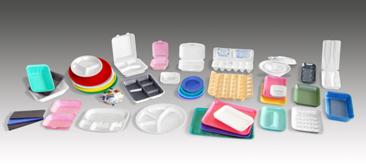
The PS foam sheet line and vacuum formers produce fine quality PS foam sheet with butane or pentane as physical blowing agent which is then converted into vacuum formed articles like trays, dishes, lunch boxes etc. The application areas are many and growing - hinged lid containers, plates, bowls, ice-cream cones, egg cartons etc. Typical product consumes only 5% plastic. It’s the most eco-friendly plastic packaging product. The wide experience in this segment ensures a diverse range of products that are well suited to meet the application, rigours of the environment while keeping in mind the overall production efficiency and flexibility. Rajoo-Commodore thermoformers, as DISPOCON- FPS are also available to the world market.
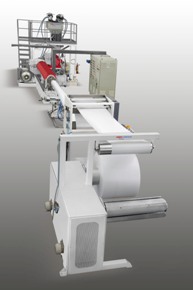
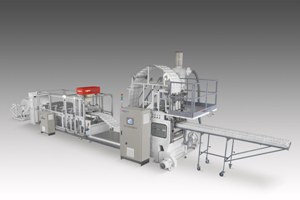
Being a pioneer in polymer foam extrusion in India, and with experience such that over 90% of cap liners and foamed banners in India are produced on the ‘FOMEX’ series blown film and sheet line from Rajoo Engineers; the company now meets with resounding success with the ‘FOMEX – FPS’ for producing PS foam.
With the sectoral growth being almost certain due to higher disposable incomes, increase in working couple population and changing lifestyle habits for take-away meals, as well as the growing installed base of our ‘FOMEX – FPS ’ Sheet lines and DISPOCON -FPS thermoformers , puts us in a formidable position of exponential growth in this sector’, says Sunil Jain, President, Rajoo Engineers. ‘Food and groceries itself constitute more than 40% of the organised retail business where again PS foam product containers will be used’, he adds.
With pioneering developments in polymer foam extrusion in India, Rajoo has emerged as the only Indian supplier for foam extrusion lines for PS and PE using both blown film and sheet extrusion process using either chemical or physical foaming. Range includes complete tandem extruder based PS foam sheet lines using circular die and gas to produce PS foam sheet and also specialised thermoformers for producing a range of disposable catering products.
About Rajoo
Based in Rajkot, Rajoo Engineers Limited, having made a modest beginning in 1986, has today emerged as an undisputed global player in blown film and sheet extrusion lines. Owing to its focused efforts in blown film and sheet extrusion lines, the Company enjoys premium market position in this segment. Being a technology driven Company, product innovations, world-class quality, state-of-the-art workmanship, increased energy efficiency, and high levels of sophistication and automation have become the hallmark of Rajoo products during all these years, positioning the Company's products on a global platform, competing with the established world leaders. With representations in many countries of the world and customers in over 53 countries, the Company's exports have multiplied after its debut in the international market in 1990. (www.rajoo.com)
For further details please contact:
Khushboo Doshi
Head-Marcom
Phone: +91 2827 252701/2/3
Fax: +91 2827 252700
Email: info@rajoo.com
Website: www.rajoo.com
News: 2009
- Indian Mfg. gets a fillip in the world market: Dec, 2009
- Excellent annual performance - 2008-09: Nov, 2009
- Rajoo's forward march as a global player in Feb, 2009
- Rajoo Engineers Ltd. at Plastindia 2009: Jan, 2009
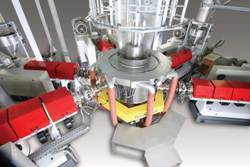
Indian Mfg. gets a fillip in the world market: Dec, 2009
Innovations in technology have always been an area of comfort for Rajoo Engineers. The commissioning of the 9th 5-Layer Fully Loaded Blown Film Line at Polypet, Nagpur, by Rajoo would go down as one of the finest landmarks in the history of Indian manufacturing of extrusion machinery. The domain of five layer blown film lines with nylon and EVOH was until now dominated by European and Canadian manufacturers, would now-on witness new market dynamics.
Polypet, Nagpur performed a thorough evaluation of all options, including the Canadian and European manufacturers, before deciding that Rajoo was the best suitor - keeping in mind product, quality, service, satisfaction with earlier supplied plant by Rajoo and an overall handholding - aspects that add immense value to the buyer, giving him confidence. With this, Rajoo Engineers now redefines barriers for barrier films used in lamination and liquid packaging, in the domestic and global markets.
The five layer plant with 2 x 60 mm grooved feed extruders for the inner and outer layers and 3 x 55 mm smooth bore extruders is equipped with a 400 mm UCD® die ( stack type with horizontal melt flow paths) and IBC system. ‘To ensure precise and accurate blend and gsm control for each material, we have successfully integrated a 14 component integrated conveying, gravimetric blending and dosing system from Germany,’ says Sunil Jain, President, Rajoo Engineers. ‘Thickness profile, another critical parameter in blown film applications is also well controlled with the state-of-the-art Automatic Profile Control System,’ he adds.
The thickness is measured using two solid state high definition capacitive sensors with 0.1 micron resolution especially designed for nylon and EVOH that are mounted on a rigid Oframe scanner which in-turn is mounted after the nip rollers, when the film is substantially cooler. The film is wound on a back-to-back dual station load cell controlled surface winder with taper tension control producing 1 m diameter rolls.
The machine is operated through an integrated touch-screen based supervisory control system for all the machine parameters such as:
- Processing temperatures
- Extruder speeds
- Melt temperature and pressure
- IBC
- Calibrating basket diameter and height
- Oscillating haul-off speed
- Material recipes
- Historical data recall, etc.
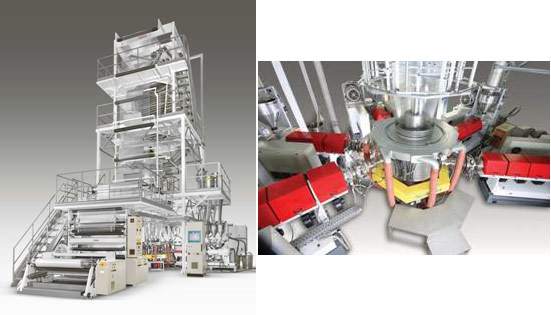
The machine effortlessly produces 75 micron barrier film with 15 micron nylon and 1010 mm layflat width, providing an output of 240 kg/hour, thickness variation under ± 4% on 2 sigma and width variation of less than ±3 mm. With this, Rajoo has again raised its bar of performance and continues launching such pioneering innovations. This commissioning has endorsed Rajoo’s leadership status in the industry. The confidence and the trust reposed by customers in Rajoo, its products and service backup is evident by the fact that Polypet who were also earlier operating a 3 layer blown film plant has ordered yet another 3 layer blown film plant scheduled to be supplied to them early next year.
ABOUT RAJOO
Based in Rajkot, Rajoo Engineers Limited, having made a modest beginning in 1986, has today emerged as an undisputed global player in blown film and sheet extrusion lines. Owing to its focused efforts in blown film and sheet extrusion lines, the Company enjoys premium market position in this segment. Being a technology driven Company, product innovations, world-class quality, state-of-the-art workmanship, increased energy efficiency and high levels of sophistication and automation have become the hallmark of Rajoo products during all these years, positioning the Company's products on a global platform, competing with the established world leaders. With representations in many countries of the world and customers in over 40 countries, the Company's exports have multiplied after its debut in the international market in 1990.
For further details please contact:
Khushboo Doshi
Head-Marcom
Phone: +91 2827 252701/2/3
Fax: +91 2827 252700
Email: info@rajoo.com
Website: www.rajoo.com
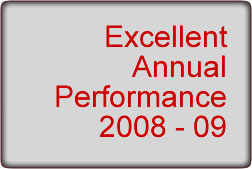
Excellent annual performance - 2008-09: Nov, 2009
EXCELLENCE IN PERFORMANCE COMES FROM EXCELLENCE IN EXTRUSION
An impressive run of years, back to back, is an indication of the resilience and leadership of Rajoo Engineers in challenging circumstances as well.
Rajoo Engineers has today emerged as an exceptional performer in India with context to growth in sales, profit and market share in the field of plastic extrusion machines.
‘The year 2008-2009 was simply an outstanding year for us – with a robust growth rate of 20% – especially when we map it with the overall polymer industry growth of 12% as well as the GDP of 6.7%’, says C N Doshi, Chairman, Rajoo Engineers Ltd. ‘Our growth is phenomenal when compared to the performance of the sector of plastic processing machinery, in general or for that matter the extrusion business, in specific’, he added.
- Numbers Speak: 2008-2009
- Sales: 5123 Lakhs (USD 11 million)
- Revenue growth : 20%
- Exports (incl. deemed exports) over 45% of sales
- Repeat orders : 60% of sales
- Growth in profit after tax: 20%
- Human Capital: 300 Rajooers
Overall market growth is no meaningful benchmark for the performers at Rajoo Engineers who have significantly exceeded this industry average figure. Numbers do speak louder than words.
‘Better comprehension of the market, competent service ability coupled with meaningful innovations in technology are attributes responsible for this position of leadership’, says Sunil Jain, President, Rajoo Engineers.
An impressive run of years, back to back, is an indication of the resilience and leadership of Rajoo Engineers in challenging circumstances as well. Increased presence across the globe, coupled with swift and synergistic penetration in newer markets are the steps taken to sustain this growth momentum.
This journey spread over 23 years has transformed the modest beginning of Rajoo to a position of market leadership and undisputable global player in the field of blown film and sheet extrusion lines. Pioneering technologies is the key feature which helps Rajoo with a distinctive and competitive edge.
About Rajoo
Based in Rajkot, Rajoo Engineers Limited, having made a modest beginning in 1986, has today emerged as an undisputed global player in blown film and sheet extrusion lines. Owing to its focused efforts in blown film and sheet extrusion lines, the Company enjoys premium market position in this segment. Being a technology driven Company, product innovations, world-class quality, state-of-the-art workmanship, increased energy efficiency and high levels of sophistication and automation have become the hallmark of Rajoo products during all these years, positioning the Company's products on a global platform, competing with the established world leaders. With representations in many countries of the world, the Company's exports have multiplied after its debut in the international market in 1990.
For further details please contact:
Khushboo Doshi
Head-Marcom
Phone: +91 2827 252701/2/3
Fax: +91 2827 252700
Email: info@rajoo.com
Website: www.rajoo.com
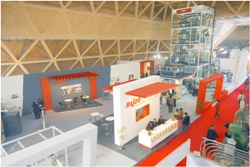
Rajoo's forward march as a global player in Feb, 2009
Rajoo's forward march as a global player in recently concluded Plastindia 2009 characterized by
Outstanding Booth
Outstanding fully loaded 3 layer blown film line in continuous operation
Outstanding RPET Sheet Line in continuous operation
Visitors entering Hall 4 at the recently concluded Plastindia could just not resist the temptation of making their first stop at the stand of Rajoo Engineers at the recently concluded Plastindia 2009. The sheer size of the booth (750 sq m) with a 52 m frontage, transparent view of the Stand with all the operating machines, an enthusiastic and active team of Rajoo sales persons …….. Who could ever resist it!
Ably supported by Rajoo representatives from Argentina, Turkey, Tunisia, South Africa, Russia and Egypt - the overseas visitors felt much at home.
Plastindia 2009, the world class plastics exhibition, now acknowledged as the second largest in the world with 1450 exhibitors including 475 from overseas provided an apt platform to Rajoo Engineers to show case technology which is world class and being demonstrated for the first time on the Indian soil.
The towering three layer blown film line operating continuously, silently and smoothly, producing 453 kgs/hour was surely the star attraction. With thickness variation of 3% on a 40 micron/1400 mm lamination grade film the giant rolls of nearly 900 kgs each with flush edges – the Rajoo plant stole a quantum leap over the competition. Christened Multifoil RECF 2370-90/1600 IBC-PI-A with extruder configuration of 2x70 and 1 x 90, lay flat width of 1500 mm, Ultrasonic sensors based IBC, multi-component gravimetric conveying with continuous blending and dosing, high output air ring with automatic profile control, fully automatic surface winder with taper tension control, trim grinders and integrated supervisory touch screen based control panel – a fully loaded plant, what more could one aspire for. Many a visitor commented –Rajoo has brought Europe to India, why visit European exhibitions now.
Also on display was a RPET Sheet line - Lamina RS1X 1490-50/800 PET, producing 250 kg/hour of PET Sheet in ABA configuration using PET Bottle flakes as the input. Complete with Crystallizer-cum-dehumidifier, 1x 90 & 1 x 50 mm extruders die lip width of 800 mm, melt metering pumps, diverter type continuous screen changers and Dual Station Center Winder. What better use one can find for PET bottle flakes and that too with affordable investment levels.
Complimenting the RPET Sheet line was a fully servo controlled thermoformer - Dispocon RETF 6535 SS, with forming area of 650 x 350 mm , maximum draw depth of 120 mm and max mechanical speed of 45 cycles/min. This model offers many advantages over the hydraulic models in terms of low wastage, precise sheet indexing and lower compressed air consumption and that too at nearly double output levels.
Rajoo also announced two technology partnerships during the show. For XPS Disposable containers with Commodore Inc. of USA. For cast extrusion stretch and PP Sheet Lines with Techno Coating S.r.l of Italy. The presence of the collaborators at the show provided an opportunity to the Indian industry to interact with them and comprehend the new technologies being introduced by Rajoo for the industry.
Commented Sunil Jain, President of Rajoo Engineers on the concluding day of the Show – “Response to Plastindia and also at our Stand is overwhelming. Where is the much talked about recession! Once again Rajoo Engineers has demonstrated that they are world class and undisputed leaders in the industry. The unprecedented response at our Stand and the keen interest in all our displayed products has provided us an impetus to march forward with more vigor”.
About Rajoo
Rajoo Engineers Limited is a 23 year-old ISO 9001 certified company specializing in the field of plastic extrusion systems and post-extrusion equipment. Rajoo Engineers is listed on the BSE. Its registered office is in Manavdar, Junagadh, with Works at Rajkot (Gujarat). Sales network is spread all over the country in Ahmadabad, Delhi, Bangalore, Chennai, Hyderabad and Pune.
For further details please contact:
Khushboo Doshi
Head-Marcom
Phone: +91 2827 252701/2/3
Fax: +91 2827 252700
Email: info@rajoo.com
Website: www.rajoo.com
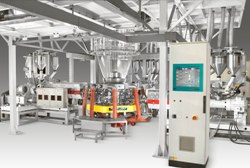
Rajoo Engineers Ltd. at Plastindia 2009: Jan, 2009
In the current global economic scenario, capital has become a scarce resource. Crash of the stock markets with squeeze on liquidity and availability of finance from lending institutions difficult, one really needs to be watchful of capital expenditure. However, plastic processors like many other industries have to continue to look forward and continue with their expansion and diversification plans optimistically.
Blown Film Extrusion – cooling marvel
K 2007 in Dusseldorf witnessed high output blown film lines by enhanced cooling technology. Now the world will experience this advance technology on the Plastindia 2009 from Rajoo Engineers but obviously at affordable price levels. Continuing their penchant for rendering technology more affordable specially for the developing economies where high capital on machinery cannot be justified, Rajoo will be demonstrating a state-of-the-art 3 layer blown film line – delivering 550 kgs/hour using a 400 mm die with binary dual flow air ring with automatic thickness control . The plant is ideal to produce all kinds of three layer films including: Stretch hood film, pallet hood shrink film, lamination grade films and liquid packaging film.
Yet another technological marvel of this machine will be the phenomenally reduced energy consumption. Energy is the second biggest component in the manufacturing cost and any savings goes straight to the bottom line. With 2 x 70 mm and 1 x 90 mm extruders, 400 mm stack die UCD® maximum layflat width of 1500 mm, IBC control system with three sensors, multi-component gravimetric gsm control and continuous blending, the plant is with fully automatic dual station surface winder with taper tension control. The total plant will be controlled through an integrated touch screen based supervisory control panel.
RPET Sheet using bottle flakes
Technology of using PET bottle flakes, which are now available in abundance in both developed and developing economies has until now been the domain of European and American machinery manufacturers. Capital investments being high, they are yet to the see the light of the day in developing economies.
RPET Sheet finds usage in a diverse range of applications – blister packaging for pharma and unit packaging, round disposable containers, hinged lid boxes, containers and list goes on.
Rajoo, known for bringing affordable world class technologies will be exhibiting a complete RPET Sheet producing system during Plastindia 2009. The system will comprise of Crystallizer, Dehumidifier, Extrusion System, Polishing Roll Stack and Winder. The system will be complete with a two extruder 1 x 90 mm and 1 x 50 mm extruder, continuous diverter type screen changer, polymer melt metering pump, ABA feed block, 800 mm die to produce 250 kg/hour of RPET Sheet of trimmed width of 700 mm. On-line trim cutting and recycling system and dual station winder to produce rolls of upto 1,000 mm are other important features of the system.
Yet once again, Rajoo is poised to maintain its leadership status in the Asian industry and towards the path of becoming a global player to reckon with.
About Rajoo
Rajoo Engineers Limited is a 21 year old Company specializing in the field of film and sheet extrusion machines and post extrusion equipment. Rajoo Engineers is listed on the Bombay Stock Exchange in India, Having its registered office in Manavadar, Junagadh and Head Office & Works at Rajkot (Gujarat). Other Regional Office are in Ahmedabad, Bangalore, Chennai, Delhi, Hyderabad and Pune.
For further details please contact:
Khushboo Doshi
Head-Marcom
Phone: +91 2827 252701/2/3
Fax: +91 2827 252700
Email: info@rajoo.com
Website: www.rajoo.com
News: 2008
- Rajoo Engineers continues to excite and impress, Oct, 2008
- An innovative barrier sheet cum blown film line: May, 2008
- Rajoo Launches India’s First Thermoformable Barrie: Mar, 2008
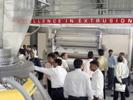
Rajoo Engineers continues to excite and impress, Oct, 2008
Continuing to walk the talk of their maxim “Excellence in Extrusion” Rajoo Engineers hosted a live show of a fully automated three layer blown film plant with 600 kg/hr maximum output and 2100mm maximum LFW, at their world class integrated facilities in Rajkot on October 1, 2008.
Attended by the who is who of film processing and flexible packaging industry from across the country and even overseas, the plant operated like a dream matching global standards producing 503 kgs/hour of 37.5 micron/2000 mm lamination grade film with 5% thickness variation at 2-sigma. The automatic winder produced huge film rolls weighing 1100 + kg and diameter of 880 mm with excellent roll geometry.
All those who witnessed this plant were highly impressed by Automation and user-friendly operating systems. A leading processor (owning a German Plant) went to the extent of saying “I feel as if am in a German manufacturing facility, both in terms of the machine quality including workmanship and the integrated infrastructure!!!”
Mr. Rajesh Doshi - MD of Rajoo Engineers Ltd. commented - “This high output plant is our unique offering to the domestic markets incorporating automatic conveying, Gravimetric dosing and blending (1+3 component) system, automatic film thickness monitoring and controlling, fully computerized integrated supervisory control panel, fully automatic surface winder with taper tension control using load cells and with automatic splicing.
Mr. Sunil Jain, President of Rajoo Engineers Ltd. addressed the gathering with a powerpoint presentation on latest innovations in plastic extrusion technology and the product portfolio of the Company. Mr. Jain emphasized the relevance of energy consumption which is the second largest cost component of the manufacturing costs. The Rajoo plant operated with a highly efficient energy consumption of 0.27 kwh/kg including all utilities. The presentation ended with an interactive Q&A session on various aspects of film processing & changes in market demands in coming years.
All the guests were exposed to the state-of-the-art integrated manufacturing facility of Rajoo Engineers Ltd.
As an icing on the cake, Rajoo bagged a prestigious overseas order for such a fully automatic blown film plant during this live demonstration.
Rajoo Engineers Ltd. is now poised to unveil a set of marvels in the forthcoming PLASTINDIA being held at New Delhi from February 4th to 9th - 2009. Do keep tuned.
For further details please contact:
Khushboo Doshi
Head-Marcom
Phone: +91 2827 252701/2/3
Fax: +91 2827 252700
Email: info@rajoo.com
Website: www.rajoo.com
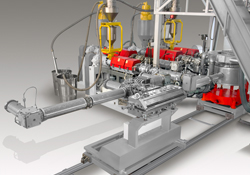
An innovative barrier sheet cum blown film line: May, 2008
Rajoo Engineers has recently completed the commissioning of its indigenously designed and developed Five Layer Barrier Thermoformable Sheet & Blown Film Combo Line at the Product Application Center in Chembur of Reliance Industries Limited. This polymer processing line is one of its kinds in the whole world.
This combo line consists of four extruders, screen changers, melt pumps, flat sheet die, Universal Co-ex Five Layer blown film die-head UCD® and fully automatic touch screen based integrated process control panel to give an output of up to 75 kg/hr. of co-extruded barrier sheets or films. The machine operates either as a sheet line or as a blown film line. Extruders are common to both the set-ups. A novel system easily converts the line from blown film extrusion to sheet extrusion set-up and vice-versa.
The line is designed to produce HIPS, EVOH and PP sheets of up to 650mm width in a thickness range from 0.2 mm to 0.8 mm and barrier blown films from 25 to 100 micron.
Being a laboratory line for testing and developing of new formulations and products, process and parameter control is of utmost significance. One of the most outstanding features of the line is its control systems incorporating Siemens Extrusion package for Plastic machinery consisting of SIMATIC application programs with screens developed using PROTOOL. HMI software allows for complete machine parameterization, drives setup, recipes, trending and alarm functions. This ensures trouble free and fully automated functioning of the sheet line giving consistent quality and output. Another equally important feature is the GSM control through European continuous gravimetric feeding system. A complete history of each product produced is also maintained which is essential for such a lab application.
According to Sunil Jain, President of the Company -”When Reliance approached us for manufacturing a Sheet and Blown combo line for their state-of-the-art Product Application Center, our technical team got enthused and once again decided to prove its passion for innovation by accepting this challenge. After all, our axiom has always been – Excellence in Extrusion”.
When it comes to selecting technically challenging extrusion lines for its world class Polymer Testing Lab, Reliance Industries Limited once again placed its trust and confidence in Rajoo, who have earlier supplied two different lines consecutively and have always excelled to surpass the expectations of this Polymer giant.
For further details please contact:
Khushboo Doshi
Head-Marcom
Phone: +91 2827 252701/2/3
Fax: +91 2827 252700
Email: info@rajoo.com
Website: www.rajoo.com
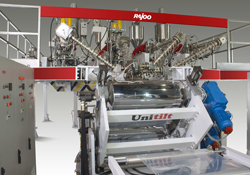
Rajoo Launches India’s First Thermoformable Barrie: Mar, 2008
Driven by India’s huge potential in food packaging and especially the barrier packaging, RAJOO has recently launched a five layer thermoformable sheet extrusion line which can produce high barrier films with Nylon/EVOH and PP/HIPS
India is a largely untapped market in thermoformed food packaging articles and with the growth of cellular families and middle class consumerism, the market for long shelf life processed food is going to grow multifold in near future.
Keeping this in view, RAJOO has recently delivered a five layer barrier sheet line to an Indian customer featuring four extruders, melt pumps, hydraulic screen changers, a Unitilt polishing roll stack and fully automatic Siemens touch screen line control to give an output of co-extruded barrier sheets worth 400 kg/hr.
The UNITILT polishing roll stack is designed for infinite adjustment from horizontal to vertical position through push button operation, thus ensuring production of variety of sheet thicknesses and polymer structures. The gap between the rollers can also be accurately adjusted thru finely threaded stud and ratchet arrangement. Digital indication of gap between the rollers adds to the ease of operation.
The line is aiming to cater to the growing markets in processed food packaging with extended shelf life and can also produce lidding foils made of various polymer structures like PP/EVOH.
The Lamina RS3X-1410/1000 is equipped with a dual stroke diverter type hydraulic screen changers with common power pack for continuous filtration of the melt through rheologically optimized flow channels which minimizes residence time and pressure drop.
The line is designed to produce co-extruded thermoformable sheets of Nylon/EVOH and PP/ HIPS in a width of 900 mm and a thickness range from 0.5 mm to 1.5 mm.
One of the most outstanding features of the line is its controls systems incorporating Siemens Extrusion package for Plastic machinery consisting of SIMATIC application programs with screens developed with PROTOOL and complete documentation. HMI software allows for complete machine parameterization, drives setup, recipes, trending, and alarm functions. This ensures trouble free operation and fully automised functioning of the sheet line giving consistent quality and output.
For further details please contact:
Khushboo Doshi
Head-Marcom
Phone: +91 2827 252701/2/3
Fax: +91 2827 252700
Email: info@rajoo.com
Website: www.rajoo.com
News: 2007
- Rajoo’s “Award Winning Stand” at Plastivision 2007: Dec, 2007
- K2007-Rajoo Establishes Credentials for Horizontal: Nov, 2007
- Rajoo's Step Forward-Launch of Range of Bag Making Machines
- Open house for 3 layer film line: Apr, 2007
- Realising Big Dreams: Mar, 2007
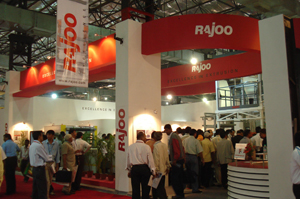
Rajoo’s “Award Winning Stand” at Plastivision 2007: Dec, 2007
Rajoo continued to make their mark in the Indian plastics industry – both in terms of innovative solutions and equally impressive presentation.
The “red” theme continued on Rajoo’s aesthetically designed Stand during the recently concluded Plastivision 2007 in Mumbai from December 6-10, 2007. The organizing committee presented the “Award Winning Stand” recognition to Rajoo.
Rajoo presented the most cost-effective and cost-efficient solution for production of T-Shirt bags , demand for which is growing at an exponential rate owing to the heavy investments by major players in organized “retail marketing”.
Rajoo’s monolayer blown film line continuously produced 250 kg/hour of 25 micron/1200 mm wide film , the highest amongst the plants displayed on the Show. Christened Foilex REHM 4090/1250 , the monolayer blown film plant with 90 mm extruder was equipped with 200 mm die and single lip air ring imported from Saturn , Canada and indigenously manufactured Sherman-Maxwell corona treater.
To match the high output of 250 kg/hour blown film, Rajoo demonstrated the 3 lane side slit-seal bag-maker operating at 250 strokes/minute to produce nearly 40,000 bags/hour. The bag-maker incorporated a high level of automation with servo controlled indexing for bag length accuracy. The machine takes a maximum web width of 1200 mm to producing gusseted bags of maximum 260 mm width.
“We have been informed that our Stand attracted the maximum visitors and it was always crowded. Industry was keen to witness Rajoo’s innovation for the Indian T-Shirt bag producers. Once again, Rajoo established its leadership and offered a solution for something so simple as producing T-Shirt bags” said President – Sunil Jain .
For further details please contact:
Khushboo Doshi
Head-Marcom
Phone: +91 2827 252701/2/3
Fax: +91 2827 252700
Email: info@rajoo.com
Website: www.rajoo.com
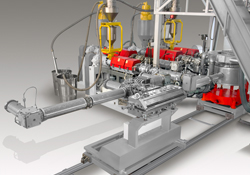
K2007-Rajoo Establishes Credentials for Horizontal: Nov, 2007
K 2007 - Rajoo Establishes Credentials – Even For Horizontal Extrusion
Visitors entering the Messe from the East Gate or those walking down from the popular Halls 16 and 17 were astonished to find a world class sheet line producing transparent thermoformable PP sheet, running full throttle at such a prestigious Show.
Rajoo Engineers Limited successfully demonstrated a world class Sheet Line at the K -2007 show in Dusseldorf last week. Now acknowledged as a global player in upward and downward extrusion blown film lines, on the K platform, Rajoo has established its credentials even for horizontal extrusion lines. The monolayer Sheet line with 90 mm extruder , produced 230 kg/hour of 300 micron thick /750 mm width highly transparent PP Sheet at the Stand continuously for seven days. Unitilt polishing roll stack the star attraction could be positioned in any axis - vertical, inclined or horizontal to produce “thin and thick” sheet (100 microns to 1.2 mm) on the same line. Christened Lamina RESP 1490/800 UT, a versatile auger crammer, continuous diverter type screen changer, Melt pump and Unitilt polishing roll stack ensured close thickness tolerance, both in the machine and traverse direction. In-line trim grinder and operator friendly SCADA based touch-screen using Siemens’s processor; the sheet line shattered the myths in PP Sheet production.
The Inverted Conical Spiral Stack Die System ( INCOSS ®) for a three layer blown film displayed right at the entrance of the Stand attracted many visitors. The 500 mm INCOSS die further established the engineering capabilities of Rajoo.
The highly aesthetic and well conceived Rajoo Stand with machines of world class workmanship won many acclaims. Visitors would stop by and ask – where is this Company from – and were shocked to receive the answer – from India. From a country known for its snake charmers, a country often epitomized by hungry stomachs, but a country also famous for its IT prowess, the country leading the BPO services boom and a country providing the backbone of all back-offices operations in the developed world.
At K 2007, Rajoo Engineers once again establishes itself as a global player – both for vertical and horizontal extrusion.
“Response at our Stand was overwhelming for the interest shown in Rajoo’s “thin and thick” , energy efficient, “value for money” Sheet Line - a unique solution to processing “ thin and thick” sheet of PP/PS/PET/PLA” said President – Sunil Jain . “More than 400 companies worldwide registered serious interest in Rajoo and most of them from the developed world which is indeed recognition of our world class technology and workmanship. Rajoo has established it credentials as a global player, now even for horizontal extrusion”.
About Rajoo
Rajoo Engineers Limited is a 21 year old Company specializing in the field of plastic extrusion machines and post-extrusion equipment. Rajoo Engineers is listed on the Bombay Stock Exchange in India. Its registered office is in Manavadar, Junagadh with Works at Rajkot (Gujarat). Other Regional Office are in Ahmedabad, Delhi and Bangalore
For further details please contact:
Khushboo Doshi
Head-Marcom
Phone: +91 2827 252701/2/3
Fax: +91 2827 252700
Email: info@rajoo.com
Website: www.rajoo.com
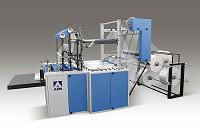
Rajoo's Step Forward-Launch of Range of Bag Making Machines
Our customers always drive us forward. When we had only Sheet Lines, our customers wanted us to build thermoformers and today we have the most successful thermoformers on the continent.
Now our customers of blown film lines want bag making machines and here we are, always listening to the fine advice of our customers.
Bag making Machines are a key resource in the chain of the plastic converting process. Being last in this chain, bag making output is Converter's "Final Product". Hence, even a minor interruption or any down time on bag making proves to be a serious bottle neck to the overall production.
After scouting around the world for the most appropriate bag making machines, we have now developed a complete range, once again with the world class technology and workmanship, which is the acknowledged hallmark of Rajoo's brand in the industry.
Once again, focusing on customer's needs, it gives us immense pleasure to launch a complete range of Bag making Machines of world class standards. These bag makers not only have Rajoo brand on it but have been developed by a team of seasoned technocrats with over 15 years of hands - on experience in the plastic machinery business and specifically bag making machines.
User friendly and value for money bag-making machines have been developed with the operator in mind, their valuable inputs have influenced the basic machine design. Microprocessor controlled and servo driven are not just jargons but features which have been used with the converter's benefits in mind, after all, it's the bottom line and product quality which is of significance.
We invite you to savor and experience the innovative range of bag making machines from the Rajoo stable to witness the effective use of technology and affordability. You are requested to witness the live demonstration of:
- Side sealing machine (AIM-800-SS servo control bag maker with 250 strokes/min)
- Bottom sealing machine (AIM-600-BS servo control bag maker with 200 strokes/min)
And this is just the beginning just a preview of what is in store for you in years to come.
We look forward to your encouragement and support.
Venue: Hall No. F-6, IPLEX 2007, HITEX Exhibition Center, Hyderabad
Dates : 27th - 30th April, 2007
For further details please contact:
Khushboo Doshi
Head-Marcom
Phone: +91 2827 252701/2/3
Fax: +91 2827 252700
Email: info@rajoo.com
Website: www.rajoo.com
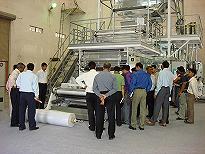
Open house for 3 layer film line: Apr, 2007
Three Layer Co-Extruded Blown Film Line
Fully Loaded with Automation
Salient Features of the line
Screw Type |
Barrier screw |
---|---|
Screw Diameter (mm) |
60 x 3 |
Screw Length (D) |
30 |
Maximum output (kg/hr) |
400 |
Screw Speed Range (rpm) |
20-120 |
Die type |
Universal Stack Die (UCD) with horizontal melt flow path |
Standard Die Diameter (mm) |
450-1.5 & 2.2 gap |
Lay flat Width Range (mm) |
750-1700 |
Film Thickness Range (micron) |
30-100 |
Line Speed (mts/min) |
10-100 |
Automation
Feed System - Multi-component gravimetric feed system
Online film thickness monitoring and automatic control system.
Cooling Control - Mechanical sensor with pneumatic control from Germany
Cooling Mode - Air chillers (instead of convention water chilling plants)
Winder Type - SAHY-LCS - load cell controlled surface winder with automatic splicing and taper tension control
Fully computerized touch screen integrated control console with processing recipe storage and report generation.
Film Structure
Film Type |
Lamination |
|||
---|---|---|---|---|
Outer layer micron |
LL-19010 (85%) |
LD-1020FA20 (15%) |
Thickness 12 |
|
Middle layer micron |
LL-19010 (75%) |
HD-F46003 (15%) |
LD-24FS040 (10%) |
Thickness 12 |
Inner layer micron |
LL-19010 (75%) |
LD-FB5026 (15%) |
HD-46003 (10%) |
Thickness 12 |
For further details please contact:
Khushboo Doshi
Head-Marcom
Phone: +91 2827 252701/2/3
Fax: +91 2827 252700
Email: info@rajoo.com
Website: www.rajoo.com
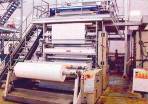
Realising Big Dreams: Mar, 2007
Touching life, everyday - such is the mission of Radha Madhav Corporation Ltd. (RMCL), an upcoming packaging company. With an impressive range of packaging products and customers spread across a variety of industries, it is not surprising that RMCL indeed touches our lives every day. Aspiring to establish itself as a complete packaging solutions provider, the company has ambitious plans to take on the world of packaging...
What started off as a consolidation of three partnership firms has carved a niche for itself, in a span of two years! And, the story does not end here; in fact it is just the beginning. Expansions are going on in full swing - for capacity addition as well as for introducing new product lines
A metamorphosis
The Daman-based Radha Madhav Corporation Ltd. (RMCL) was formed as recently as in January 2005. However, the business itself is more than 10 years old, as RMCL is the result of the metamorphosis of three firms - Mayura Industries, Radha Madhav Industries and Metro Poly Prints. The consolidated business basically offers primary packaging and secondary packaging, with an Rs.220-crore gross block.
In the more than a decade-old journey, RMCL has serviced more than 400 clients. These are spread across India and abroad, and encompass industries like FMCG, pharma, food & spices, cosmetics & personal care, confectionery, milk & milk products, infrastructure, cement, textile & garments, etc. Thus, one of its current strengths is the good relationship maintained with such a large number of clients.
We know all our clients directly, and we know their packaging requirements, which make it easy for us to offer products or solutions according to their needs, said Mitesh Agarwal, Managing Director & CEO, RMCL.
Agarwal, who has taken the mantle of the company from his father and founder of the company, is steering RMCL in the right direction. While embracing the latest technologies, he didn't forget to build a team with the right attitude. I have a team of people, who have been with the company since its inception. So, there is the synergy required to accomplish our ambitious future plans, added Agarwal.
Product lines
A company driven by technology, RMCL has state-of-the-art facilities for the production of primary packaging and secondary packaging. Primary packaging is again divided into flexible division and folded carton division, while secondary packaging includes products like liners, specialty thermoformable films, cartons and various profiles for different applications.
With in-house manufacturing of barrel cast and blown films, metallization arrangements, lamination, gravure coating, extrusion coating, and good printing facility; RMCL presently manufacturers surface printed barrier films, metalized films, laminates, wrappers, overwrap films and lamination films of various types. It also manufacturer's multi colored printed mono cartons of very high quality. Calendar films of pharmaceutical packaging form a soon-to-be-added product line.
RMCL also commands leadership in secondary packaging with a product portfolio comprising stretch cast films, BOPP tapes, masking film, soft blister films, commodity liners of various materials like PE, PVC and PP.
As of now, food & beverages packaging forms the major share in RMCL's revenue. With the new Uttaranchal unit getting ready for production, the company plans of enter pharmaceutical segment as well. About 60 per cent of our product will be in pharmaceutical packaging and close to 30 per cent will be in food packaging. I believe revenue is better in pharmaceutical segment, but at the same time cost is also little higher, added Agarwal.
All under one roof
The company proudly claims itself to be capable of making any type of cast and blown polymer films - as the customer wants. Granules are bought from Reliance, IPCL, DuPont, etc. Purchasing is made in economies of scale, which controls the cost.
The laminates produced by the state-of-the-art machines are of high quality, and are less costly as compared to the competitors products.
Solvent-based and solvent-less lamination facilities are available. One, three, five or more layered laminates can be made as per the barrier properties required by the customer. A tandem extrusion line is being installed currently. The gravure and flexo printing lines meet the customers printing needs as well. The flexo line is a comparatively new addition, which offers better registration and cost savings for customers of flexible packaging.
A recently installed machinery makes 10-12 heat-shrinkable poly film called double bubble film, a replacement for PVC films. The double bubble film can be used as a secondary packaging to pack a set of bottles, for instance, in pharmaceutical packaging. This film will cost only 60 per cent of PVC film. A new pouch packing machine will be installed soon for food products.
Barrier properties of films can be enhanced by silica coating, i.e., silicon oxide and aluminum oxide coating on transparent films. These films can be used in place of aluminum foil. RMCL has silica coating facility, where the coating is continuously monitored and controlled to maintain the right thickness of 1-2 . There is also the facility for wax coating for soap wrappers.
RMCL has all the technology under one roof - be it flexo or gravure printing, solvent based or solvent-less lamination, etc. The choice is up to the customer, but guided by the able professionals.
In an attempt to further improve the service offered to its customers, RMCL is in the process of implementing SAP. It will go live by April 2007. SAP will enable the customer to track the progress of the order placed with us. This is being done for the first time inIndia. With this, we will be a part of the customer supply chain,beamed Agarwal.
A tactful approach
Visibly proud of RMCL's strong and diversified customer base, Agarwal explained the company's strategy, Our strategy is to build a long-term relationship with the customers, and be flexible enough to meet their varying needs. Most of our machines are meant for smaller production runs. However, we maintain a certain production quantity to manage it economically. This gives us an edge over our competitors. We are ready to supply to anyone if the profitability is 15-16 per cent.He proudly stated that when sourcing their packaging requirements from RMCL, the customer is not paying more, but getting more benefits.
Some fine examples
Retail packaging for food is one of the areas, where RMCL has made inroads. The recently launched Reliance retail chain uses RMCL's poly films for its pulses, cereals, etc. The company has developed a film, where printing can be done directly on the film. This is called surfaces printing film. There is an option to laminate the film, i.e., a printed polyester film laminated to a barrier film. This film supplied to Reliance retail stores is completely recyclable, cheaper and gives the effect of laminated films. Currently, the volumes may not be high, but we know it will pick up in the future. By supplying according to the customer's qualitative and quantitative needs, we remain their preferred customer's,elaborated an enthusiastic Agarwal.
Another interesting packaging material developed by RMCL is in the industrial packaging sector, again for Reliance. Recron 3s is a state-of-the-art reinforcing material from Reliance, which is used to increase strength in a variety of applications. For example, Recron 3s acts as secondary reinforcement in concrete which arrests cracks, increases resistance to impact / abrasion greatly improves quality of construction. For Recron 3s, RMCL has developed a paper-based packaging, where the paper dissolves in water within two rotations of the concrete mixture.
About 60 per cent of our product will be in pharmaceutical packaging and close to 30 per cent will be in food packaging - Mitesh Agarwal, managing director CEO, RMCL.
The paper has to withstand all the pressures in the transit, sale and distribution network. At the same time, when it is thrown into the concrete mixture, it has to tear off and get dissolved in the mixture. The paper we developed initially had a very thin coating of PE material. But, Reliance wanted a further thin coating and we modified the material and reduced the amount of coating. We offer surface printed films and, laminates in various structures. So, as per the varying budgets and aesthetic needs, we have developed almost five products for Recron itself. And, we regularly supply these five products. The quantity per order may be small, but we value our relationship with Reliance, as with our all other customers, explained Agarwal.
Expanding horizons
RMCL is carrying out expansion of manufacturing facilities for existing and new products. A new unit in Daman is in the final stages and it will be ready by March 2007. This until will add to the production capacity of existing product lines, i.e., BOPE high end barrier shrink film, coated films, and laminated structures / wax-coated structure / contoured and shaped pouches. The machinery has been imported from Italy and Korea, where the company has technical support to produce world-class products. BOPP films will be produced in India for the first time and the company will enjoy monopoly position in the sub-continent.
Meanwhile, the new plant in Uttaranchal will manufacture packaging for solid drugs, liquid syrups, creams and ointments of both Rx and OTC nature. This includes blister packs for tablets and capsule, collapsible tubes with PVDC coating, etc. The PVDC coating is to be offered for the first time in India by RMCL. The new plant will follow international quality standards like HACCP and GMP. Blisters will be produced in-house in hygienic conditions, right from the granules. Technically high-end calendar films will be used, on which even minute printing can be done. This is quite critical in pharmaceutical packaging. There will also be provision for label printing. The new facility will be ready by May 2007, and production is slated to start in June 2007.
In the pharmaceutical sector, we have at least 50 existing clients. As of now, we are supplying them our other products. Now, we have started the legwork of supplying PVC blister products. Since we are already supplying to the pharmaceutical industry, we don't expect any problem in marketing the new product, explained Agarwal.
While talking on the new R&D project, Agarwal said, Earlier, major R&D work was done by our collaborator in Italy. Our in-house facility was capable to modify the quality to some extent, which was good enough so far. However, to keep up with our growth plans, a dedicated R&D centre is also being established for developing high-tech packaging products for pharmaceutical industry.
On a positive note
We believe in offering next-generation products, while keeping in mind the price-sensitive Indian market. And, we want to position ourselves as a complete packaging solutions provider, concluded Agarwal, while sharing his dream of RMCL to be known as more of a packaging advisor than a product manufacturer.
For further details please contact:
Khushboo Doshi
Head-Marcom
Phone: +91 2827 252701/2/3
Fax: +91 2827 252700
Email: info@rajoo.com
Website: www.rajoo.com
News: 2006
- Seven Layer Blown Film Line: Nov, Oct,2006
- Focusing on premium Indian Processors: Jun,2006
- India moves from PS to PP: Jun,2006
- Innovation Lifeline: Apr, 2006
- Innovation at display during Plastindia 2006: Mar, 2006
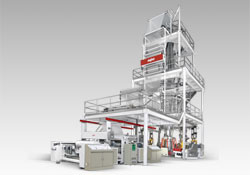
Seven Layer Blown Film Line: Nov, Oct,2006
Rajoo Engineers offers seven layer blown film line - Multifoil with 2 x 60 mm grooved feed extruders and 5 x 55 mm smooth bore extruders with 500 mm INverted COnical Spiral Stack type die - INCOSS. It has a maximum gusseted lay-flat width of 2800 mm / winder width of 2100 mm and plant output of 600 kg/hr for non-barrier films and 350 kg/hr for barrier films. It incorporates ultrasonic sensor based IBC system; multi-component dosing and gsm control, automatic thickness control and B & R processor based integrated computerized supervisory control system. The seven layer film is primarily used for producing barrier films for packing of long shelf life edible products like oil, pasta, meat, etc.
For further details please contact:
Khushboo Doshi
Head-Marcom
Phone: +91 2827 252701/2/3
Fax: +91 2827 252700
Email: info@rajoo.com
Website: www.rajoo.com
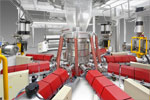
Focusing on premium Indian Processors: Jun,2006
In terms of technology and automation, we have always maintained a leadership status and the demand by the Indian processors for such levels of machinery is evidence of their acceptance to REL as compared to imported machinery says Chandrakant N. Doshi, Chairman, Rajoo Engineers, in dialogue with ET Polymers.
Q. Overall how do you see the movement of the extrusion machinery market Do you see this trend continuing
We have an extremely bullish view of the Indian plastics industry and of the plastic machinery business in India. Per-capita plastics consumption as compared to the world average is still miniscule which itself is a reflection of the high potential.
Plastic processors in India are today exposed to high levels of technology and automation in plastic machinery and are willing to invest and pay a premium for the same. The advantages of high automation for improving quality and reducing wastage parallel to increasing economies of scale is being well understood.
In terms of technology and automation, we have always maintained a leadership status and the demand by the Indian processors for such levels of machinery is evidence of their acceptance to REL as compared to imported machinery. The globalisation and demand for energy efficient extrusion machinery has made the market bloom and the upward trend will continue for the new vistas to open ahead in flexible packaging automobiles and agriculture.
Q. What do you see as Rajoo's key strength to address the market needs?
Adapting to market requirements, leadership in terms of bold innovations, world-class workmanship and efficient after-sales-service.
Q. 1988 to 2006, can you take us through the evolution of Rajoo Engineers in the extrusion business?
Major milestones for Rajoo (firsts in the Indian industry) are:
1990 - Launched the first ever Blown film to manufacture chemically foamed PE films and displayed the line at Plastindia.
1991 - Co-extrusion feed block for Multilayer Sheet Extrusion Line
1994 - Introduced the first ever indigenously designed and developed Oscillating Haul-off system for blown film lines and displayed at Plastindia 1994
1995 - Extruder with grooved feed bush
1995 - Wide width blown film plant with lay-flat width of 3 m
1996 - Exported country's first "CE" marked machine to the most demanding European market and since then there had been numerous exports to Europe.
In terms of technology and automation, we have always maintained a leadership status and the demand by the Indian processors for such levels of machinery is evident of their acceptance to REL as compared to imported machinery.
1997 - Introduced an internal bubble cooling system for blown film lines and displayed at Plastindia 1997
1999 - Secured ISO 9001 certification
2000 - Introduced in Asia, a stack type Universal Co-Extrusion Die christened UCD. The die was displayed on Asia's first ever five layer co-extrusion blown film manufactured and displayed the line at Plastindia 2000
2001 - World's highest output TQPP blown film line - 140 kg/hr
2002 - Electro-hydro pneumatic plug assist thermoformer with in-mould cutting for PP and PS containers
2003 - World's first two layer TQPP film line - launched in Plastindia
2003 - Launched the Three Layer Blown film Line with digital IBC and a Fully Automatic surface-gap-center Winder with an output of 450 kg/hr and displayed the line in Plastindia 2003
2004 - Displayed the first ever two layer downward extrusion PP blown film plant on the "K" platform and that too with a Dual Turret Fully Automatic Surface / Gap / Center winder christened FLEXIWIND DuTplus
2005 - Debut into Germany - Developed a CE compliant high output Three Layer sheet line for processing PET regrind at the rate of 700 kg/hr and exported the same to Germany.
2005 - Three Layer Blown Film Plant for heavy duty FFS Film - supplied to Iran.
2005 - Five Layer Blown Film Plant successfully commissioned at Skypack, India - fully loaded with ultrasonic IBC, gravimetric dosing, Dual Turret Automatic Winder
2006 - INverted COnical Spiral Stack Die INCOSS with a Seven Layer Blown film Line - launched during Plastindia 2006
2006 - Wide width 1200 mm dia multilayer stack type die displayed at Plastindia 2006
Q. Which are your main product categories today?
Our main product categories are:
Foilex - Monolayer Blown Film Lines
Multifoil - Multilayer Blown Film Lines
Lamina - Mono and Multilayer Sheet Lines
Aquaflex - Mono & Multilayer Downward Extrusion Blown Film Lines
Fomex - Blown and Sheet extrusion lines for foamed products
Dispocon - Thermoformers
Q. Which new areas of diversification / growth have been identified?
Our growth strategy will focus on the following:
Increased exports of high tech products and increasing footprint
Targeting premium Indian plastic processors to give them the advantages of high technology and automation in plants supplied overseas
High levels of automation both for process control and quality consistency
Further improving after-sales-service
Further improving process know how and product development support to our customer
Develop cast film lines
Exports today constitute 70% of our sales turnover, which is the highest amongst plastic processing machinery manufacturers in India.
Q. What export initiatives have Rajoo embarked on, with what success?
Exports today constitute 70% of our sales turnover, which is the highest amongst plastic processing machinery manufacturers in India. Our export strategy focuses on the following issues:
High quality of after-sales-service (assured response in 24 hours)
World class workmanship
World class technology
High level of automation
Increasing footprint - Europe, Latin America and Asia-Pacific
Q. How important is after-sale support in this industryWhat are your unique deliverables?
It plays a very critical role in this industry. Our unique deliverable is:
Using inputs from repute brands available anywhere in the world
Comprehensive operating and maintenance manuals
Turnaround time of less than 48 hours - to any customer query
Ex-stock spares delivery
Q. Has R and D played a pivotal role is your successCan you briefly highlight on your R&D infrastructure?
With a dedicated team of 20 highly qualified engineers (the highest amongst the industry), recently we have taken the following initiatives:
Tools:
3 D model solution
Rheological simulation
Focus Areas:
High output PP sheet line using increased percentage of regrind
Increased levels of automation to improve product quality and consistency
Screw designs for specific materials and requirements
Improved melt flow paths depending upon applications
Q. Please highlight features of your 7 layer blown film plant?
A seven layer blown film plant with 2 x 60 mm grooved feed extruders (inner and outer layer) and 5 x 55 mm smooth bore extruders for producing seven layer barrier film structures. The heart of the machine is a 500 mm "INverted COnical Spiral Stack" die - designed and developed by Rajoo, a first for any Asian plastic processing machinery manufacturer.
With maximum lay-flat width of 2800 mm, the winder width is 2100 mm fore reels of 1000 mm diameter on a fully automatic center-surface-gap winder with load cell based taper tension control and five motor systems with guillotine knife. It's a high output plant (500 kg/hr for non-barrier) incorporating an ultrasonic sensor based IBC system, fully loaded with the highest level of automation every witnessed by the Asian industry. Multi-component conveying gsm control system, an automatic thickness control system and integrated computerized supervisory control system are other capabilities of the machine.
Q. Are you facing more competition from Indian companies or international companies?
At the entry level, low automation products, we do face competition from Indian companies but customers today are willing to pay a premium for quality, technology and workmanship. In the overseas markets, we encounter competition with the world players and we are able to offer value for money.
For further details please contact:
Khushboo Doshi
Head-Marcom
Phone: +91 2827 252701/2/3
Fax: +91 2827 252700
Email: info@rajoo.com
Website: www.rajoo.com
.jpg)
India moves from PS to PP: Jun,2006
Equipped with an 800 mm die and 90 mm extruder for processing PP, with 50% regrind material, the line has an output of 230 kg/hr. "Overall there has been a shift from PS to PP for thermoforming of disposable containers because of the advantages the material offers.
The increased availability, lower prices, lower density compared to PS and the face that it is microwaveable and can handle hot products, are factors that have contributed to this shift," explained Sunil Jain, President of the company. The line incorporates a Maag melt pump and a continuous diverter type automatic screen changer and thickness monitoring system from German company Folitec.
Even so, the sheet line is not a new introduction from Rajoo. "We predicted that this would be the trend and were one of the first to develop specialist sheet lines for processing and thermoforming PP about four years ago," claimed Sunil. In fact, the latest line is an upgrade from an earlier introduction that had an output of 140 kg/hr. "The trend now is towards higher capacities," he added. The line was displayed with a hydraulically operated and computer programmable thermoformer "that has minimum mechanical parts and is considered to be the best in the industry."
The 21 mould cavity thermoformer was operating at 25 stroke / minute producing 30000 parts / hour. When asked if Rajoo's sheet line sales have been confined to the Indian market, Sunil replied, "No. A major breakthrough for us has been in Myanmar where we have supplied a sheet line and thermoformers for processing both PS and PP. We have also supplied a line to Persian Plastics in Iran.
For the production of pallet hood shrink and stretch film, Rajoo has introduced a three layer blown film line Multifoil RECF 2360-90 / 2100 IBC. "With an output of 400 kg/hr, the line incorporates all the automation features of the seven layer blown film line unveiled at Plastindia show," said Sunil.
The Indian manufacturer has also added gravimetric blenders to each extruder (from Germany based Plastcontrol), central hot air extraction systems on each extruder and a 500 mm INverted COnical Spiral Stack type die (INCOSS). Also included is an automatic profile control air ring, oscillating thickness scanner, gusseting arrangement operating with an oscillating haul-off, center-surface-gap winder and a Plastcontrol computerized supervisory control with touch screen panel.
According to Sunil, the company is also working on introducing another innovation, which is a three layer wide width blown film line Multifoil RECF 2312 / 4200. "The line is an order from an Indian processor who is in the business of container liners. With 120 mm extruders and 1200 mm INCOSS, the line is capable of producing a thickness of 0.2 mm and 5000 mm open lay-flat, with provision for gusseting, at an output of 600 kg/hr," explained Sunil.
For further details please contact:
Khushboo Doshi
Head-Marcom
Phone: +91 2827 252701/2/3
Fax: +91 2827 252700
Email: info@rajoo.com
Website: www.rajoo.com
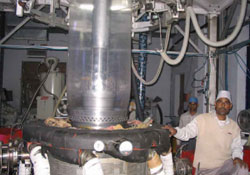
Innovation Lifeline: Apr, 2006
"Our forte is in innovation. It is only by understanding the requirements of the medical / pharmaceutical industry have we been able to develop specialty packaging," said Naresh Kumar, Managing Director. "One example is the coated breathable paper that we developed for packaging syringes some years back. We should have had it patented because it has now become standard packaging in the industry," he proclaimed. Under controlled pressure, the coated paper allows ethylene oxide (ETO) gas to permeate it, enabling syringes to be sterilized. "It took us 18 months to develop it, but we succeeded in formulating the right structure," said a beaming Kumar.
The company has many more successful applications to its credit: like the thermoformable film made up different plastic materials, which was developed without a tie layer. Then there is the self-peelable, aluminum based PE film laminate that was developed to replace surface printed coated aluminum foil for surgical blade packing. "The previous packaging was not only expensive but since it was surface printed it was prone to scratches. Also, the foil could not prevent oxidisation. Being a life saving device, we saw a need to develop a solution that would be able to protect the blade inside the packing plus allow for gamma sterilisation," explained the founder of the company, who is an engineer by profession.
Having been involved in plastics since 1973, Kumar is no stranger to the packaging industry. "The plastics business in India was very new at the time when I set up the first company, Skylab Industries; to supply injection molded rigid packaging. Amongst our first few customers were Dabur, Niki Tasha, Hammer Flask and Hindustan Syringes (still a customer of ours today)." In 1985, the company expanded its business to include the manufacturing of blank video cassettes. "With the start of cable television, the business nosedived and we decided to diversify. We had to keep up with the rapid changes in technology and move on," he explained.
But the changeover from rigid to flexible packaging must have been something of a blessing in disguise as Kumar says they have not looked back since 1993 when the new business took off. "At first we were only processing 300 kg of material a day but the business has grown by more than 10% every year," he added, explaining that a Windsor three layer PE line was bought in 1996 followed by an extrusion coating line and a three layer cast sheet line to produce blister packs for disposable needles and syringes. The company made its largest capital investment last year when it purchased a fully automatic, high speed eight color rotogravure printing machine and a five layer Rajoo Engineers blown film line.
Already, Skypack has lined up a number of developments that will be manufactured using the new technology. According to Kumar, "We intend to market specialty films like high barrier PVDC coated and heat sealable films, sealable / peelable films for pouches, cups and trays as well as EVOH and nylon based and anti fogging films." But before Skypack is able to commercialize its new products, it has to educate the cost sensitive domestic market. Kumar says he has handed over this daunting and challenging task to the marketing team, headed by his son Naveen Talwar. "He not only has to oversee new developments but also be able to convince the market that the products are more aesthetic, functional and, in the long run, more cost effective," explained Kumar.
Quipped Naveen, "We have started promoting transparent, high barrier films that can go through metal detectors without any problems, unlike metallised PET or foil." Others include metallised PE to replace MET-PET and clear, high stiffness film for bags. Since it is able to offer equivalent barrier protection and is a more environmentally friendly alternative to PVC sheet, thermoformable PET sheet is also being promoted. He claimed that Skypack was the first Indian company to have had successfully developed thermoformable webs based on PETG, Barex and GAG. "Though these environmentally friendly, self heat sealable sheets are a novelty in the market, there have been no takers so far," lamented Naveen. "One reason cold is that the packaging machinery for processing these sheets requires modifications, which means additional costs. Unfortunately, most local packaging companies are not prepared to take the risks - if one company is willing to take the lead, the rest will eventually follow! It is just a matter of time before companies realize the benefits of our films," he opined.
Though comfortably ensconced in the medical / pharmaceutical sector, Skypack is expanding its horizons to food packaging. "Barrier films for prolonged product shelf life are catching up in India," said Kumar, adding that with its stack die design Rajoo's five layer blown film line allows the possibility of extending the number of layers to seven. Skypack has already supplied five layer barrier films for oils and is working with an OEM supplier on a specialist film for packing coffee.
Other projects include a sealable / peelable film with good hot tack and the ability to withstand steam sterilisation. This will be used in DuPont's Tyvek HDPE fiber protective material, which is commonly applied by the apparel, construction and medical industries.
"Processors should be ready to meet the challenges. We believe that with our technology in place and a stable production, we are ready," stated Kumar. Having chalked up a turnover of Rs.250 million last year, Kumar says the company is on track to staking its claim as one of the leading producers of packaging materials in India.
For further details please contact:
Khushboo Doshi
Head-Marcom
Phone: +91 2827 252701/2/3
Fax: +91 2827 252700
Email: info@rajoo.com
Website: www.rajoo.com
.jpg)
Innovation at display during Plastindia 2006: Mar, 2006
Touching the roof of the Hall, the 15 m high seven layer blown film plant was the talk of the Show. Overall Rajoo made a major impact at the Show through magnificent display at the Stand and around the Show ground with splashes of the now well recognized Rajoo logo in red.
Fully supported by representatives of various European and American automation systems suppliers at the Stand, Rajoo established its capability to integrate world class systems in the Indian design and manufactured sophisticated seven layer blown film line.
The seven layer blown film line operated smoothly on four days of the show, producing both nylon and EVOH based barrier films and LD / LLD based lamination grade films. The fully automated surface / gap / center 2100 mm width winder producing 1000 mm dia rolls with automatic roll changer over established the top of the class design.
Christened - Multifoil RECF 2760-55 / 2100 IBC - the seven layer line with 2 x 60 mm grooved feed extruders (inner and outer layer) and rest 5 x 55 mm smooth bore extruders was equipped with the 500 mm INverted COnical Spiral Stack type die (INCOSS). The high output plant (550 kg/hr for non-barrier films and 350 kg/hr for barrier films) used an ultrasonic sensor based IBC system from D. R. Joseph of U.S.A. The plant was fully loaded with the highest level of automation ever witnessed by the Asian industry.
Multi-component conveying and gravimetric dosing system for Doteco, Italy and an Automatic Air Ring (Smartlip) with capacitative thickness sensor from Octagon, Germany and B & R processor based integrated computerized supervisory control system. Incorporating Corona treatment from the best manufacturer in the world - Sherman of U.K. and Digital Center Line based web guiding system with width measurement from BST Sayona. A confirmation of world class suppliers' confidence in the capabilities of Rajoo by leading their established brand names to Rajoo.
Also on display was a 1.2 m dia three layer INCOSS die with a matching Dual Lip Air Ring for a wide width three layer plant to produce film for bulk packaging - container liners, woven sack liners.... Yet once again, a first for the Asian industry.
With the ever increasing market acceptance of PP as compared to PS for disposable containers, Rajoo took another step forward in technology - a monolayer Sheet Line with 90 mm extruder for PP using 50% regrind - an output of 230 kg/hr. Sheet Line incorporated a Maag Melt Pump and a continuous Diverter type automatic screen changer and thickness monitoring system from Folitec, Germany. Clarity and precise thickness control was very well appreciated by visitors.
To go hand in hand with the Sheet Line was a Thermoformer, acknowledged the best thermoformer in the industry today. With minimum mechanical parts, the hydraulically operated, computer programmable Thermoformer used a 21 cavity mould operating at 25 strokes / minute producing nearly 30000 glasses per hour.
The visitors to the Show did acknowledge that the Indian plastics industry has come of age and Rajoo is leading from the front in the plastic processing machinery sector. A matter of immense pride for the Asian industry.
For further details please contact:
Khushboo Doshi
Head-Marcom
Phone: +91 2827 252701/2/3
Fax: +91 2827 252700
Email: info@rajoo.com
Website: www.rajoo.com